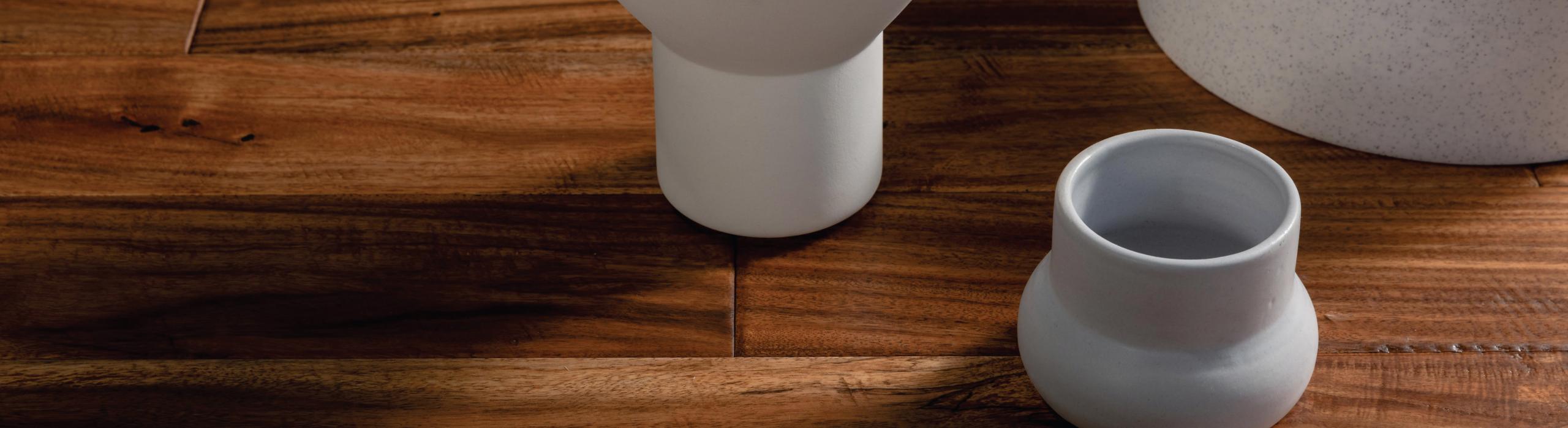
CHOOSING YOUR KENTWOOD FLOOR
CHOOSING YOUR KENTWOOD FLOOR
A collection of tips and tools to help you choose your Kentwood floor.
Buying a hardwood floor is a big decision, so we’ve developed some helpful tools to make the process easier – and help you choose the Kentwood floor that’s perfect for your home.
First: know that every Kentwood product is manufactured to our own exceedingly high standards of product quality, so which ever style you choose, the quality is a given. But remember: all Kentwood products are made from real hardwood, which means every piece will have a unique appearance.
FAQ
Many condo councils have regulations regarding the installation of hardwood flooring. One of the most common is that an acoustic underlay be installed under the wood flooring to minimize sound transmission between floors. Check with your council to find out what specific requirements they may have. Your Kentwood dealer can recommend a suitable underlay.
There are four basic installation techniques for hardwood flooring.
1. Nail Down – the boards are fastened to a plywood subfloor using cleats or staples
2. Nail Down with glue assist - the boards are fastened to a plywood subfloor using cleats or staples along with adhesive. This method is recommended for floors 4 ¾” and wider in width
3. Glue Down – the boards are glued to the subfloor with a special wood flooring glue
4. Floating – the boards are glued to each other, but not to the subfloor below. The entire floor ‘floats’ on a cushioned underlay.
5. Glueless – a popular variation on floating installation in which the boards have a specially designed joint system that allows the boards to be ‘clicked’ together without glue or fasteners.
Many people choose a wood species based on its hardness, thinking that a harder wood will be more durable and resistant to wear and damage. While this is true to some extent, the fact is that all hardwoods can be dented and scratched, even with the toughest finish. So it’s more important to choose a floor based on its visual appearance.
All hardwood species used in Kentwood flooring are suitable for the purpose, so it’s better to choose a species and color that suits your individual lifestyle and tastes. For example, generally speaking lighter colored floors and heavier grained woods like oak will be more forgiving of daily wear (dust, footprints, etc) and will require less maintenance than darker floors and clear grained woods like maple. Exotic woods tend to be less tolerant of changes in climate than domestic woods.
Most styles of Kentwood engineered floors are approved for use over radiant heat. (Solid wood floors, and certain wood species such as hickory and acacia, are not suitable for use with radiant heat systems.) There are some special considerations when installing over radiant heat and the temperature of the floor must be kept within recommended levels to avoid damaging the floor. For more information, consult the installation instructions.
Hardwood has been a popular flooring material for centuries and continues to be the flooring material of choice for many good reasons.
It’s durable – well-made hardwood floors can last a lifetime and longer. While the initial cost may be higher than with other types of flooring, hardwood’s longevity makes it an excellent long term investment.
It’s comfortable – real wood has a natural warmth that no artificial material can replicate and makes a very comfortable living surface.
It’s uniquely beautiful –hardwood has a beautiful appearance and, as a natural material, every piece will be completely unique.
It’s a great Investment – real hardwood adds value to your home.
It’s authentic – real wood has special value and appeal over artificial materials.
It’s sustainable – wood is a naturally renewable resource.
In a solid wood floor, every board is made from a single solid piece of hardwood. This is the most traditional form of hardwood flooring. It is installed over plywood subfloors using nail down installation.
In engineered flooring, every board is made from several layers of wood, with valuable hardwood used only for the surface, or ‘wear’ layer. The other layers may be plywood, common softwood or even high density fiberboard (HDF). Engineered floors are generally more stable than a solid floor, and they are more versatile too, as they can be installed in practically any situation with a variety of different installation techniques.
Laminate floors are made with entirely manufactured materials and contain no real wood (although the main component of many laminate floors is HDF, which is a wood-based product). Laminate floors have an image of wood (or other material) imprinted onto the surface, to give the appearance of a wood floor.
First, let’s look at what all three have in common.
- All are manufactured to the same stringent quality standards
- All are subject to the same rigorous quality control oversight
- All meet or exceed strict standards for air quality
- All have a high performance finish that meets our exacting specifications
Now for the differences.
The biggest differentiating factor is the veneer, the hardwood surface layer that is what you see and walk on. In an engineered floor, only the top layer is valuable hardwood; the rest of the floor is composed of lower cost plywood or softwood lumber.
Three factors affect the value of the veneer:
- The wood species itself; rare and exotic woods are costlier than more common types
- The cutting method; veneers may be sawn, sliced or peeled. For more info, go here.
- The overall thickness of the veneer layer.
Veneer thickness varies widely throughout the industry and is seldom highlighted, but it’s a very important component of the floor’s performance in addition to its appearance. Here’s why.
One of the factors affecting a hardwood floor’s long term performance is its ability to be re-finished when the original factory finish begins to look worn and dull, or becomes damaged in some way. There are two basic methods of re-finishing:
- Re-sanding, in which the original finish is sanded away, leaving the hardwood veneer exposed. A new finish is then applied to the entire floor. In order to be re-sanded, the floor must have a veneer of at least 2.5mm thick.
- Re-coating, in which the old finish is ‘primed’ and a new coating of finish is applied over the old one. Veneers of any thickness can be re-finished.
Here’s how the three Kentwood sub-brands compare: (show three profiles for illustration)
Couture: Our high-end custom home collection
- Sawn veneer
- Veneer thicknesses 3.8mm - 4mm*
- Re-Sandable
Kentwood Collection: Our mid to high-end collections
- Sawn veneer
- Veneer thicknesses greater than 2.5mm*
- Re-Sandable
Abode: Value priced collections targeted to builders
- Veneers may be sawn, sliced or rotary peeled
- Veneers thicknesses 2mm or less*
- Re-Coatable
*Nominal measurements
Please note that all veneer measurements are nominal, with a possible variation of +/- 0.2mm on most Kentwood products. Sanding and any texturing processes may introduce some slight variation into the overall thickness of the wood over the length of the plank or between planks. The micro bevel edge allows for smooth transitions between installed boards so the fractional variations do not impact use.