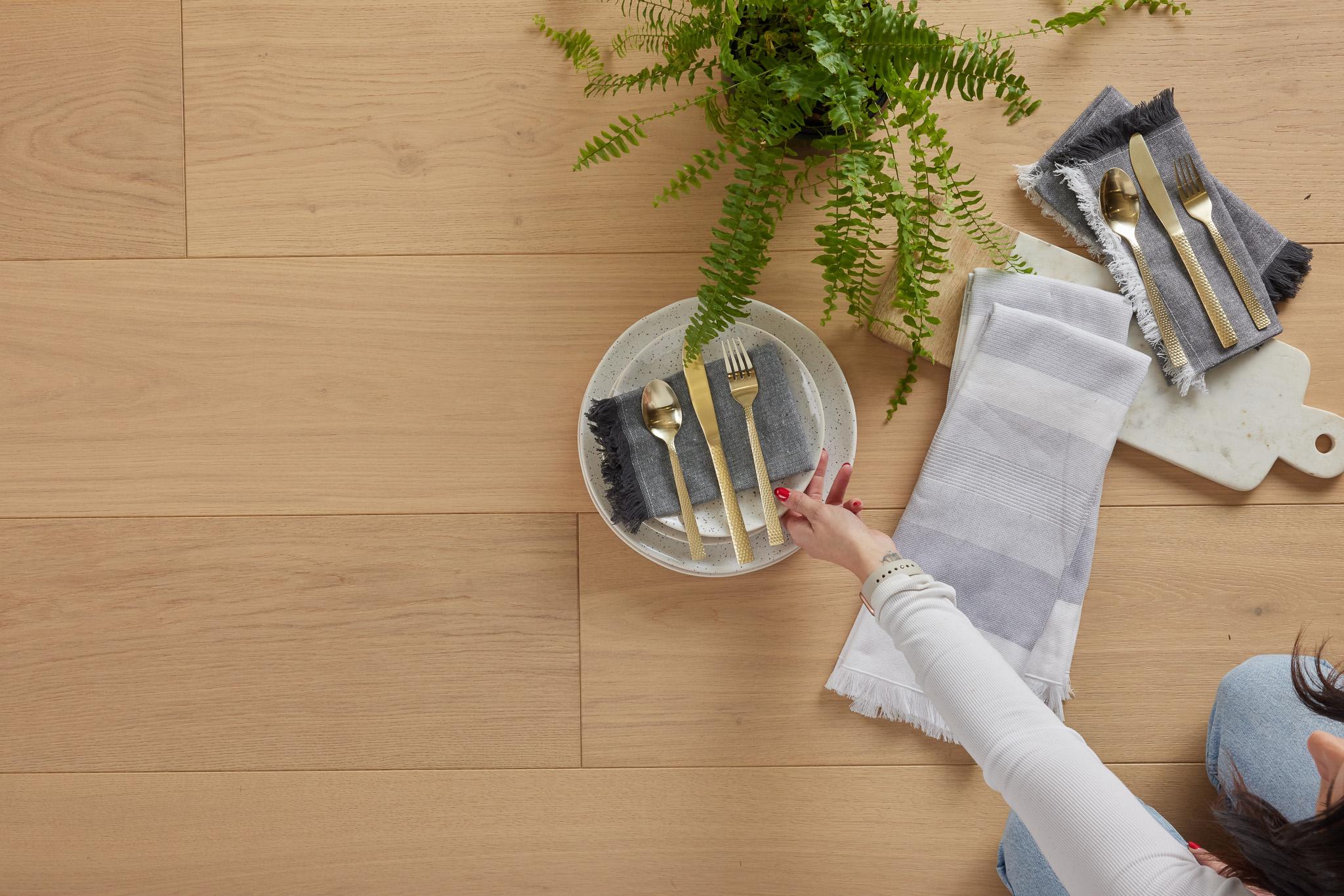
HARDWOOD FLOOR FINISHES
HARDWOOD FLOOR FINISHES
HOW TO ASSESS THE QUALITY OF A FLOOR'S FINISH
The factory finish applied to hardwood flooring is one of the most important factors in ensuring the long-term performance of the floor. Assessing the comparative merits of different manufacturers’ finishes can be difficult as marketing materials frequently emphasize details that don’t really indicate the quality of the finish. Comparing different products’ warranties is not much help either; virtually all prefinished hardwood floors offer very similar product wear warranties.
So how do you as a consumer assess the quality of a floor’s finish? By giving you some insight into the finishing process, we’ll provide some knowledge to help you make an informed decision. We’ll start by understanding the purpose of the finish, and then explain a bit about our ‘secret recipe’ that helps ensure the best possible performance of every Kentwood floor.
THE ROLE OF THE FINISH
The purpose of the finish is quite simple: to protect the hardwood surface while ensuring that the wood itself can be seen with maximum clarity and fidelity. A well-formulated finish will protect the floor from: - Surface moisture that could adversely affect the wood - Wear and tear from the abrasion of day-to-day foot traffic - Minor mishaps like scratches, spills and stains The primary ingredient in a floor finish is polyurethane, a synthetic resin that is applied as a liquid and ‘cured’ to a hardened state. Polyurethane is used widely in many different manufacturing processes to create a protective surface. In the case of flooring, various additives can be added to the polyurethane to give it additional properties. One of the most common is aluminum oxide, which makes the finish very durable and resistant to wear through. Other additives are used to give the finish properties like scratch and stain resistance, hardness and flexibility, visual clarity, and more. Most of these properties can be measured using internationally-recognized ASTM tests, making it easy to accurately assess how well the finish formulation is doing its job.
THE KENTWOOD FINISH FORMULA
The Kentwood finishing process begins with a list of specifications, defined standards of performance in several categories such as those listed above. We work with two of the leading finish manufacturers in the world – PPG Coatings and Klumpp Coatings – to formulate a finish ‘recipe’ that will meet our specifications. As Kentwood floors are made in several different facilities with different finishing equipment, we ‘tweak’ the recipe, customizing it to ensure that the specifications are always being met on every product.
THE MORE THE BETTER?
Many flooring manufacturers emphasize how many coats of finish they use, but more does not necessarily mean better. In addition, because different layers convey different properties, the strategic arrangement of the layers can also have an impact on the overall performance. The key to obtaining the best finish performance is the appropriate combination of coating layers applied in the appropriate quantity (measured by grams per square meter) arranged for maximum effect. With this approach, a finishing line with six coating applicators can achieve the same or better results than a finishing line with ten applicators.
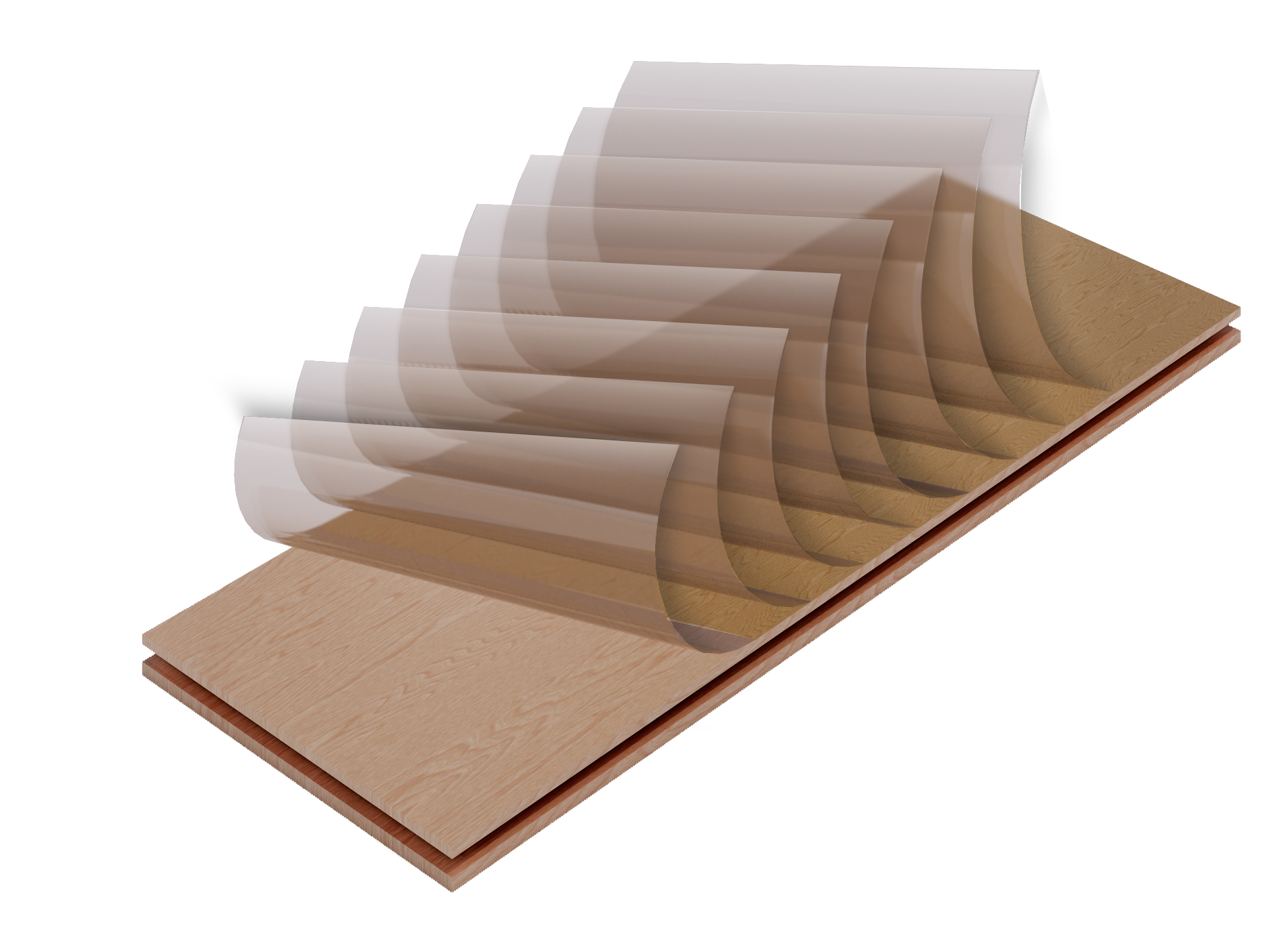
Kentwood floors are typically finished with seven or eight coating layers, including some ‘high-performance’ layers with special sealing and strengthening properties. This produces an excellent finish that out-performs many competitors’ products and has proven itself in the many thousands of homes where Kentwood floors have been installed over the past 20+ years.
TEST, TEST AND TEST AGAIN
To ensure the performance of our finish, Kentwood floors undergo one of the most intensive testing regimes in the industry. First, we have Quality Control inspectors at every facility monitoring the finishing process to ensure it is done correctly. Samples of finished flooring from every production run are sent to the finish manufacturer for testing; we document and save all the test reports for future reference. Finally, we send random samples of finished product to our own lab facilities for further testing to ensure the coating meets our standards.
YOU BE THE JUDGE
When assessing a flooring finish, here are three simple questions to ask your dealer: - What properties does the finish offer? Is it a comprehensive list? - Who manufactures the finish? Is it a recognized third-party manufacturer? - How – and how often - is the finish tested to ensure it is meeting the performance specifications? These questions are harder to answer than ‘how many coats of finish are there’ but they will give you a clearer picture of what’s protecting your new hardwood floor.